Why It Matters
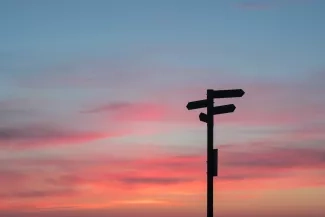
Photo by Javier Allegue Barros | Unsplash
The Institute for Healthcare Improvement (IHI) white paper, Whole System Quality: A Unified Approach to Building Responsive, Resilient Health Care Systems, proposes a holistic approach to quality management — whole system quality — to help organizations close the gap between the quality that customers currently receive and the quality they could be receiving. The following excerpt from the white paper discusses the theoretical context for whole system quality and compares key quality management approaches.
While several quality management models (e.g., total quality management, Lean management, Training Within Industry, high-reliability organizations) resemble the whole system quality (WSQ) approach, WSQ aims to integrate the best aspects of each to build a common approach. Many practitioners will recognize the combination of Quality Planning, Quality Control, and Quality Improvement components in the whole system quality approach as a “quality management system.” Total quality management (TQM), the dominant approach historically used in health care, is less commonly used today in the US but still has proponents in Europe. TQM is more heavily rooted in Deming’s thinking and emphasizes his 14 Points for Management as a roadmap for leaders. Organizations using the TQM approach may devote more attention to developing managers and leaders who can coach their staff according to these principles by, for example, focusing on ensuring all staff have at least some improvement training and can thus contribute to continuous improvement in the organization to achieve the highest possible quality.
Many elements of TQM continue to inform Lean management, which is commonly used in health care today to manage quality. In reality, Lean management and TQM are similar and share common intellectual influences (e.g., Deming, Juran, Toyoda, Ohno, Ishikawa, Shewhart). Lean management is rooted in the Toyota Production System, with a focus on standardized work at all levels, organization by “value streams” to improve flow and make timely work delivered to the customer a central motivator, and continuous attention to building improvement capability in staff at all levels. Organizations implementing Lean and TQM use many of the same diagnostic tools to understand the nature of process problems (e.g., forms of Pareto analysis) and many of the same measurement tools to understand variation over time (e.g., run charts, control charts).
Training Within Industry (TWI) — a set of approaches to build and teach standard work, first used in the US for workforce remobilization during World War II — also had significant influence on quality, though with less application in health care. This approach focuses on building standard work to simplify jobs, building a foundation for constant scientific learning, and ensuring rapid training. Today, the TWI approach informs many Lean management applications, especially TWI’s focus on building standard work.
A high-reliability organization in health care puts safety at the center, with a focus on building a culture where everyone in the organization understands how their job contributes to safer patient care. In practice, the management approaches adopted in high-reliability organizations (e.g., huddles, standard work, rigorous measurement) are similar to those adopted by Lean organizations, and many organizations today implement tools and practices from both approaches.
The various quality management (QM) methods may each have a different focus and use distinct, but overlapping, sets of tools, but they still share many similar features:
- A focus on the customer as the definer of quality;
- A set of tools to effect continuous quality improvement at a system level, rooted in scientific thinking, comparing actual performance to predicted performance, and then analyzing gaps to inform action; and
- Some reference to the need to link quality to customer demand and, in this sense, linking customer needs directly to strategy.
Which Approaches Are Most Effective?
The published literature shows mixed results for most of these quality management approaches. For example, reviews of Lean interventions in health care find overall positive effects on quality, efficiency, and staff engagement. Studies over longer periods of time show positive impacts on quality and cost, but analysts note the poor quality of many studies. Overall, more studies analyze the impact of Lean tools rather than Lean transformation as a unifying management approach. Individual organizations adopting Lean as a wholesale approach to management and leadership transformation have noted significant improvements. For example, after a period of losses, Virginia Mason Health System reported positive margins every year since implementing the Virginia Mason Production System and received recognition as a Leapfrog Top Hospital in numerous years.
The literature on total quality management shows similarly mixed impacts. Some research suggests that essential practices for TQM success (e.g., staff empowerment, systemwide focus on quality improvement, customer focus) have a mixed effect on total performance, with stronger evidence for impact on clinical outcomes than on the system as a whole for other elements of performance (e.g., efficiency, overall competitiveness). Researchers note obstacles to success using the TQM approach include poor employee engagement, lack of leadership support, and inadequate training. They cite leadership engagement (not just passive support) and the transition from a top-down management style to a more collaborative approach with managers and staff as crucial to longer-term success.
Similarly, reviews of the high-reliability organization (HRO) model find that the overall quality of evidence is low, but also find positive impact on process measures (e.g., reporting of safety measures) and outcome measures (e.g., total serious adverse events) with this approach.
In general, the effectiveness of the various QM approaches in health care has not been studied with a high level of rigor, perhaps because health systems adopt these approaches to address practical problems, often without relationships to formal evaluators. Each method has predictable benefits based on its relative focus (e.g., safety, waste reduction, employee-driven quality).
It is not least for this reason that IHI does not advocate for using a single approach, but rather for incorporating the best and most common aspects from each quality management method to offer the whole system quality approach as a unifying framework. Whole system quality embraces many of the cultural principles adopted by TQM organizations, the management practices adopted by Lean organizations, and the focus on defect reduction and the linkage between culture and safety advanced in HROs.
To learn more about whole system quality — including a description of how whole system quality links to customer needs, organizational vision, and quality strategy — download Whole System Quality: A Unified Approach to Building Responsive, Resilient Health Care Systems.
You may also be interested in:
What Does It Mean to Rethink Quality?
Shaping the Transition to Whole System Quality: Examples from the Field